The Origins and Craftsmanship of Clone Rolex Watches
Where are replica Rolex watches made? Continue reading to discover more about the brand and the locations in Switzerland where Rolex watches are crafted.
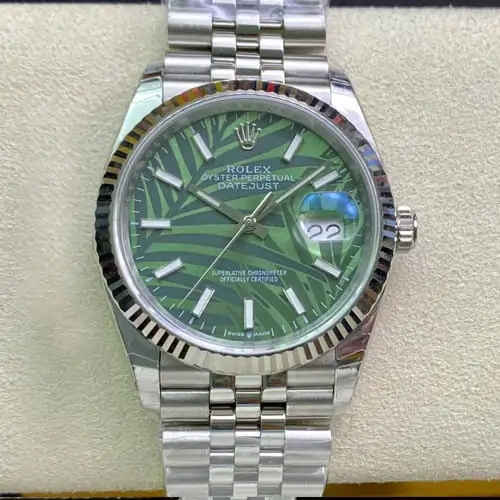
The Heart of Rolex: Geneva Headquarters
Rolex stands as a beacon of luxury worldwide, achieving an unmatched level of acclaim through its commitment to quality and innovation. Behind every Rolex watch’s precision lies an intricate production process, utilizing cutting-edge facilities and the finest technical expertise across several Swiss locations. Although Rolex’s heart is in Geneva, the creation of its components spans the country, reflecting a blend of tradition and modernity. For those exploring the prestigious world of Rolex on a budget, our selection of affordable Rolex watches offers a gateway into this esteemed legacy without compromising on the excellence the brand is known for.
Nestled in the Les Acacias neighborhood of Geneva, the Rolex World Headquarters serves as the epicenter and beating heart of the entire company’s global operations. Constructed in 1965, these state-of-the-art facilities display Rolex’s signature green colors across multiple buildings that house vital functions. This includes the Executive Offices where the Board of Directors chart Rolex’s visionary course at the highest levels of leadership. Research and Development departments based here pioneer the innovative technologies that continuously redefine luxury watchmaking.
Les Acacias’ responsibilities extend well beyond Swiss soil. The World Headquarters coordinates international distribution, marketing, and advertising to uphold Rolex’s global aura. Client services and technical support provided from Geneva offer real-time assistance worldwide. Modern tools like the Rolex Virtual Concierge replicate the in-store experience online.
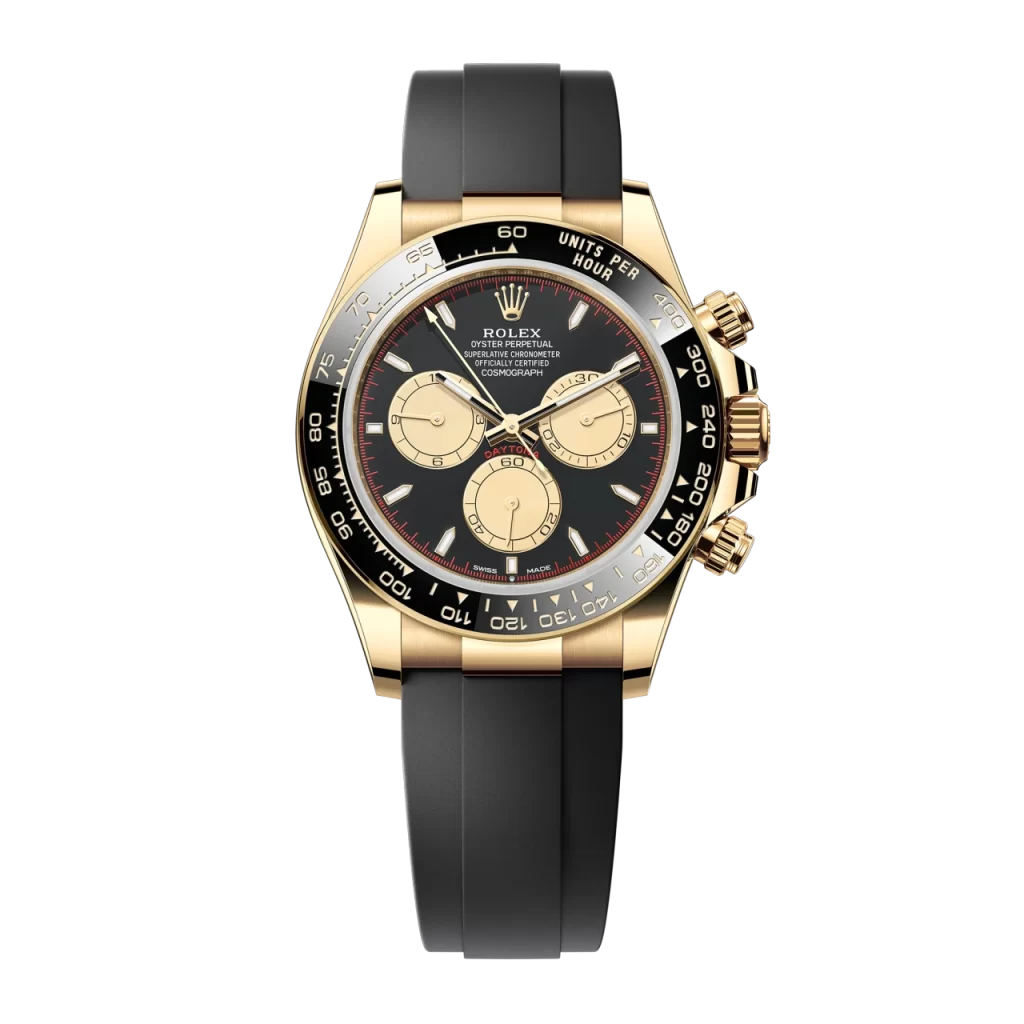
United by a passionate commitment to excellence, Les Acacias perpetuates Rolex traditions while constantly improving them. The mechanisms driving style, quality, and cutting-edge performance all originate within these very walls. In many ways, this Geneva facility does not just manage Rolex’s worldwide success – it manufactures it. When wearing a Rolex, it is but a small piece of Les Acacias on every owner’s wrist. The innovation, unrelenting precision, and timeless luxury built into that iconic Rolex watch all bear the Swiss seal of approval conferred at the Rolex World Headquarters.
The Movement Factory: Bienne
Tucked along the Bienne Lake within the peaceful Swiss canton bearing its name, Rolex’s expansive Movement Factory has been producing mechanical movements for the world’s finest watches since the early 2000s. Housing state-of-the-art facilities equipped with ultra-modern tools, the ambitious premise reflects Rolex’s future-facing ethos – where cutting-edge technology merges seamlessly with generations of watchmaking expertise. Complex, multi-level production lines occupy vast shop floors to engineer mechanical movements of the highest precision. Computerized manufacturing via advanced robotics forms the base calibers, while seasoned technicians perform intricate finishing and decoration by hand, upholding Rolex’s blending of human craft with boundless innovation.
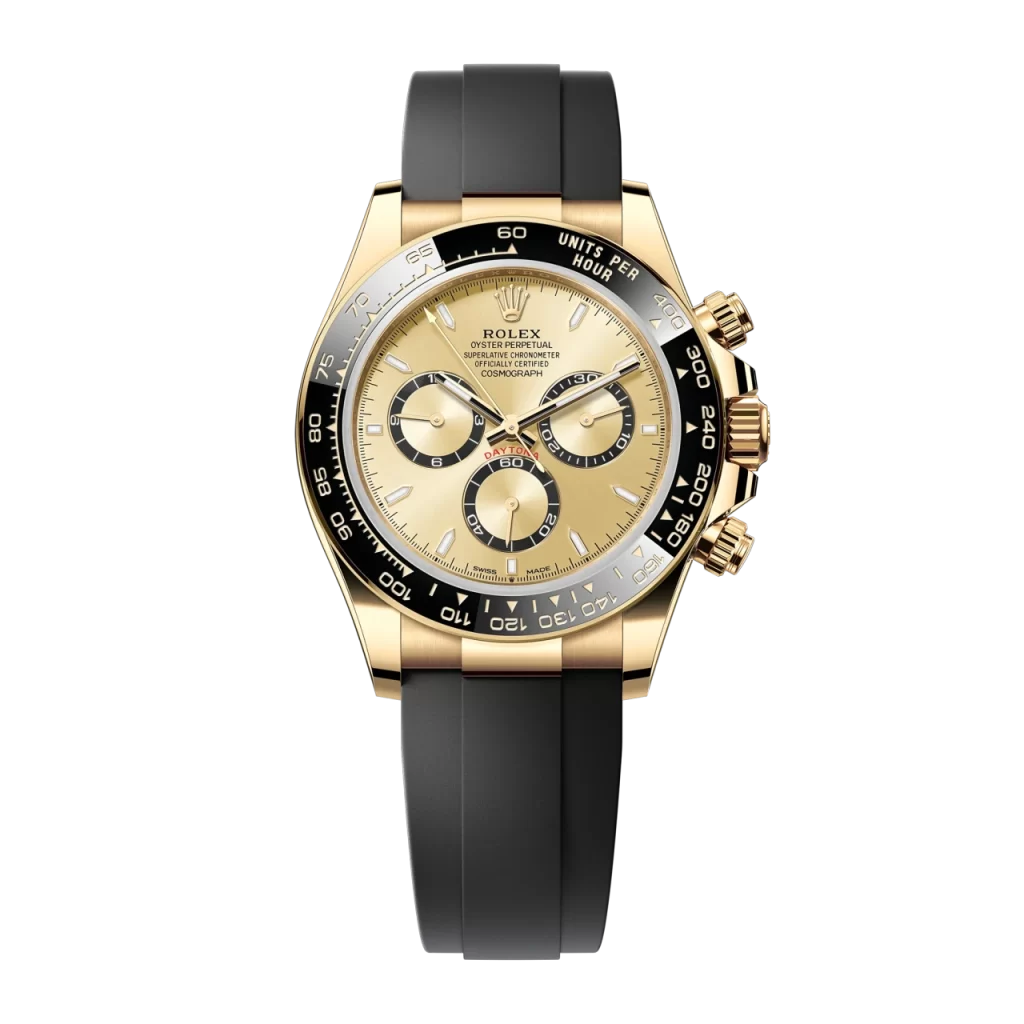
Every mechanical self-winding movement across clone Rolex‘s collections takes shape here – from the iconic 31xx to the new-age 32xx Calibres. Fitted across Daytona chronographs or Sea-Dweller divers, these ‘beating hearts’ must perform perfectly every second. Such flawlessness stems from Rolex’s vertical integration, with Bienne developing core components like the calibers, patented Paraflex shock absorbers, and paramagnetic blue Parachrom hairsprings completely in-house.
Supporting facilities allow comprehensive testing for shock-resistance, waterproofness, and reliability to guarantee excellence. By owning the entire production process of the all-important mechanical movement, Rolex retains complete control over quality and performance. Bienne’s output provides that critical edge, embedding the driving force inside every luxurious Rolex model from machined plates and gears to final timing certifications.
Crafting Cases and Bracelets: Plan-les-Ouates
In the Geneva suburb of Plan-les-Ouates lies the ultra-modern Rolex facility dedicated to producing one of the most instantly recognizable components of their watches – the case and bracelet. Sprawling over 58 acres, the Rolex Centre of Excellence for Creating Cases takes vertical integration to new heights, with capabilities for everything from foundry to final polish. The complex journeys raw metals undergo here transform them into signature fixtures of the Rolex persona. Forging masters shape strong, corrosion-resistant alloys into Oyster cases guarding delicate movements. Machining workshops cut them to flawless proportions before expert hands lovingly polish each surface through multiple stages. Likewise, exquisite Rolex Jubilee and Oyster bracelets take form by mingling advanced robotic construction with delicate hand-assembly.
Plan-les-Ouates provides Rolex complete mastery over creating cases and bracelets matched in quality only by their movements. The intricate steps feed into their hallmark methodology – merging state-of-the-art technology with generations of Swiss artistry. Within these very walls lies the genesis of those iconic fluted bezels and graceful center links which circle countless wrists as badges of luxury worldwide. Each glinting case and bracelet is a reminder of Rolex’s relentless pursuit of perfection alive and beating in Plan-les-Ouates.
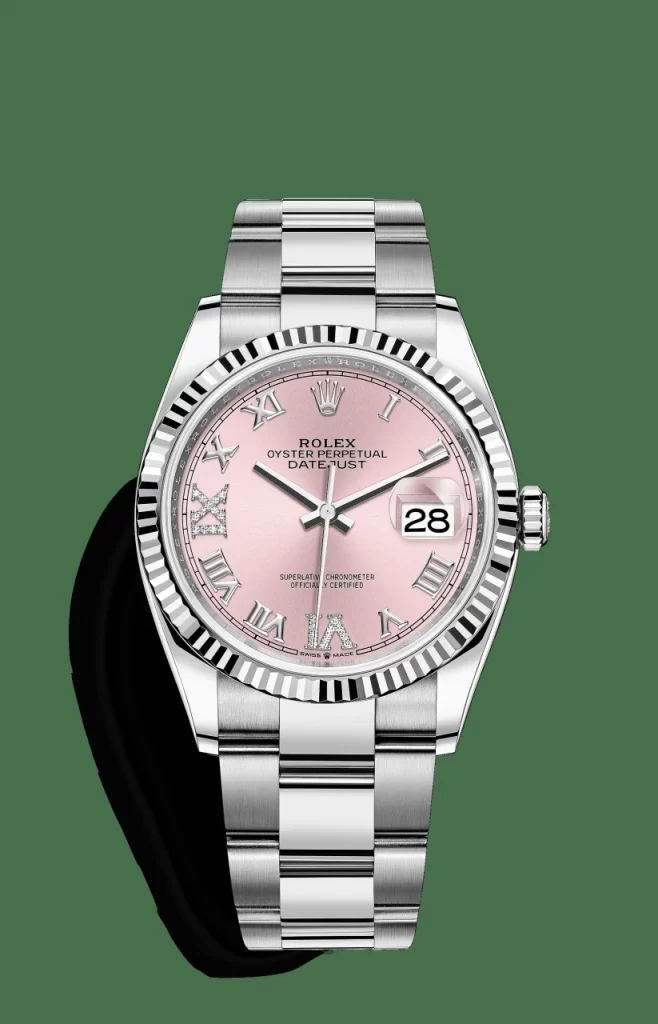
The components crafted here ultimately travel back to their Geneva HQ for final assembly into the world’s finest time machines. But the raw power lending shape, waterproofing, and magnetism to those watches springs forth from these formidable Swiss facilities designed for one sole purpose – creating the substance at the heart of the Rolex legend.
The Art of Watchmaking: Chene-Bourg
Tucked within the scenic Swiss commune of Chene-Bourg lies Rolex’s specialized atelier devoted to the creative facets of watchmaking – gem setting and dials. Within meticulously maintained workshops, expertise in these intricate crafts passes down generationally from master to apprentice. It is an environment tailor-made for the flourishing of human artistry and technique – where diamond setters and dial makers practice ancient arts still perfected by hand today.
Behind secured doors, gemologists of the highest order meticulously select and set thousands of diamonds, sapphires, and rubies to jewel-encrusted watches. Crafted by hand, the gem-set Rolexes showcasing these ateliers’ talents dazzle from windows of the maison’s Geneva boutique. In Chene-Bourg, vocational dial makers add personality to watches expressing individual style and character. Lavish dials ranging from meteorite to malachite emerge incorporating intricacies like engraving or miniature enamel painting.
By centralizing centuries-old expertise around gems and aesthetics, Rolex retains firm oversight on rare handcrafts defining luxury. The dazzling, pavé-set bezels or the shimmering dark-green dials rarely proclaim their origins. But those finishing touches granting unique personality may very well trace their roots back to Chene-Bourg, where imagination and artistic vision tick effortlessly in tandem with Swiss tradition.
The Rolex Oyster Case
When Hans Wilsdorf set out to create the perfect watch, one of the biggest challenges was protecting it from dust and moisture. Dust and moisture can cause problems like clogging and oxidization if they infiltrate the watch’s casing. Together with Aegler, the company in Bienne that would become the primary Rolex manufacturer, they developed a waterproof wristwatch to meet the challenges of everyday wear and tear.
The Submarine, created in 1922, was the first of these efforts. It was the first of its kind by being attached to a hinge inside a second, outer case. This outer case utilized a bezel and crystal screwed down to create a watertight seal. The Submarine was Wilsdorf’s first step towards producing a waterproof watch.
The Submarine’s dual-case design became known as the Oyster Case and was patented as such in 1926. Its design and winding movements ensured a hermetical seal that protected the watch’s inner chamber from outside elements. The name came from the animal itself, with Wilsdorf citing its ability to remain underwater without damage.
Wilsdorf decided to put his creation to the test in a way that only Rolex could pull off. He learned that Mercedes Gleitze was about to set a world record by becoming the first British woman to swim across the English Channel. He asked her to carry an Oyster with her along the journey to demonstrate its durability and waterproofness. Upon finishing the swim, the Oyster was revealed to have kept good time and made a statement to all.
The bezel for the Oyster watch was fluted, meaning it could be screwed down onto the middle case using a special tool exclusive to Rolex watchmakers. As time went on, so did technological advancements in watchmaking. The bezel eventually advanced to become rotatable and fitted, making it popular with divers’ watches.
A fine fluting technique is applied to the back of the Oyster case, allowing it to be screwed down hermetically to the middle case. Many current divers’ watches in the Rolex inventory have a case back made of either Oystersteel or 18 kt. gold.
On the original Oyster case, the crown was screwed down onto the middle case. Rolex later introduced the Twinlock winding crown in 1953. This was the year the famous Rolex Submariner watch was launched, becoming a staple in the divers’ watch category that still sits atop the throne today.
This system featured a patented double seal. In 1970, the system was further enhanced with an additional sealed zone reinforcing the waterproofness of the product.
Rolex has a reputation to uphold, which is why each of its products goes through rigorous testing protocols before being bestowed with the famous Green Seal.
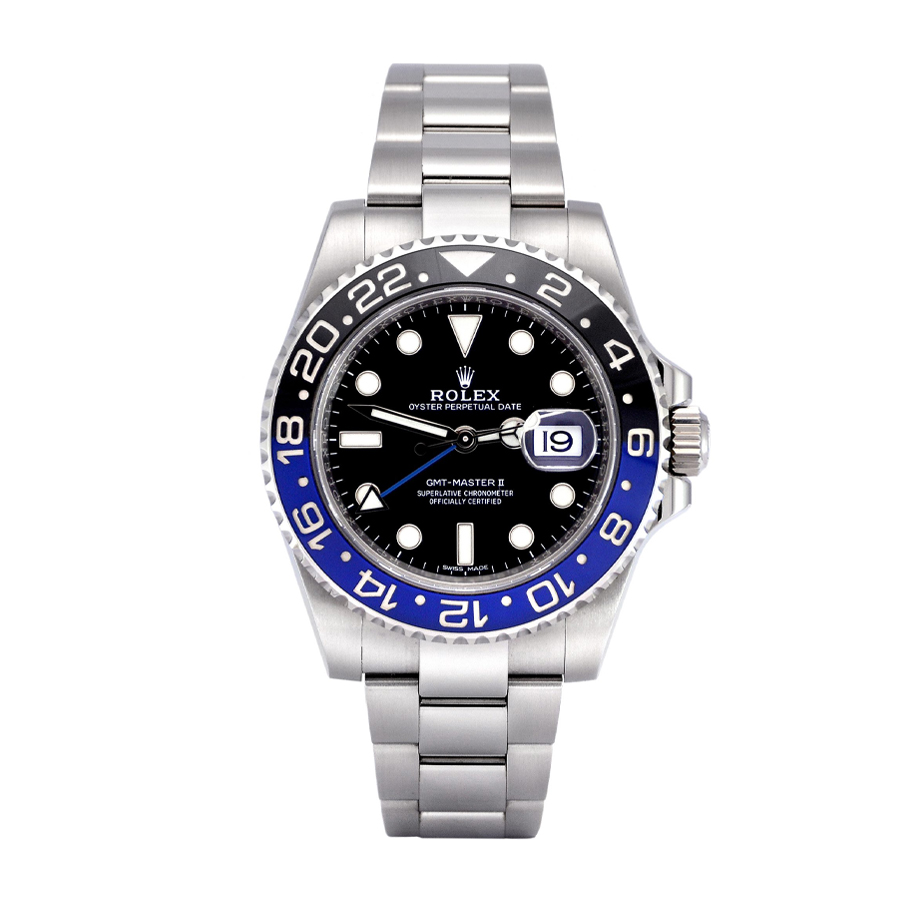
The modern Oysterlock system, fitted on most Professional replica Rolex models from https://ashleyout.com/replica, undergoes 26 different types of drop tests before leaving the production facility. This helps ensure protection against accidental knocks and gestures as well as climbing summits with altitude or diving to great depths with pressurization.
The clasp system is tested by submerging the watch in a tank of chlorine and salt water. Sand is then added to the mixture and the clasp is opened and closed tens of thousands of times to ensure smooth functionality with each locking and unlocking.